以前こちらの記事『【報告書の書き方】品質保証初心者-3』で不具合(不良)報告書の書き方を記載しましたが、その中でも『発生原因』と『流出原因』について悩む人は多いのではないでしょうか。
初めて作成するときは、言葉の違いが分かりにくくどういう意味なのか悩むこともあると思いますが簡単な事例を合わせて紹介します。
不具合発生メカニズム
まず、簡単に不具合発生のメカニズムについて紹介します。
製品の製造工程が正常であれば正常品が作られます。
しかし、工程上に異常要素が入ってしまうと不具合品が作られます。
異常要素を入れないことが根本的な不具合対策になります。
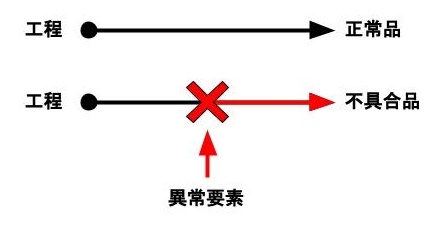
発生原因とは
異常要素が入ったことが不具合の発生した原因になります。
では、なぜ異常要素が入ってしまったのか?を分析していく必要があります
流出原因とは
発生した不具合品を後次工程で発見できず流出してしまった原因になります。
なぜ発見できずに流出したか?を分析していく必要があります
社内で発見される場合もあれば、社外で発見される場合もあります。
時間軸で考えると『発生原因』は一時的なもの(点)で『流出原因』は継続的なもの(線)になります。
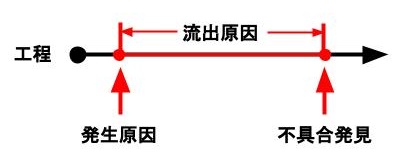
事例 カレー作り
カレー作りを例にご紹介します。
下記8工程を各工程異なる担当者が担当することします。
1. 材料皮剥き
2. 材料切る
3. 材料炒める
4. 水加える
5. 煮込む
6. ルー入れる
7. 煮込む
8. 完成
事例-1 具材の切り方が違う
■発生状況
材料を切る工程で切り方を間違えた→加工間違い
■発生原因
作業指示書(レシピ)の確認不足
思い込みで作業した
■流出原因
材料を切った後で切り方を確認していない
鍋に入れる際に、材料の切り方を見ていない
事例-2 材料に火が通っていない
■発生状況
材料を炒める(もしくは煮込む)時間が短い→時間間違い
■発生原因
作業指示書(レシピ)の確認不足
タイマーの時間設定を間違えた
火力設定間違い
コンロ設備に異常はないか
忙しくて業務処理のため意図的に調理時間を短くした
■流出原因
火が通った確認をしていない(材料の見た目・色、串等での材料の固さ確認)
事例-3 味が薄い
■発生状況
水の分量が多い(もしくはルーの分量が少ない)→分量間違い
■発生原因
作業指示書(レシピ)の確認不足
計量間違い
計量機器に異常はないか
■流出原因
味見をしていない
まとめ
簡単な事例と共に『発生原因』と『流出原因』の違いについて理解できたでしょうか?
発生状況によって、『発生原因』と『流出原因』も異なりますので参考になれば幸いです。
コメント